Building a Logistics Foundation with the Ultimate Mission of Ensuring Supply Stability
Core Principles
The Otsuka group handles products that relate directly to human life, including pharmaceuticals, foods and beverages. As such, we ensure the rigorous control and maintenance of product quality throughout distribution, and actively take measures to ensure stable supply in the event of a natural disaster or other emergency situation. The group also promotes environmentally friendly logistics operations through measures, such as reducing CO2 emissions.
The Otsuka group company Otsuka Warehouse takes a lead role in delivering products throughout Japan and handling a part of overseas logistics. Otsuka Warehouse has established a quality policy aimed at providing a level of quality that earns the trust of customers and society. All employees are fully on board with our policies and comply with all provisions to maintain and improve quality.
Otsuka Warehouse Quality Policy
- We will pursue safe and secure services that reflect changes in the environment and social needs, and provide a level of quality that helps us earn the trust of customers and society.
- We will appoint quality officers at the head office and all offices to maintain and manage quality.
In addition, we will formulate targets for quality for each business site and implement an action policy to achieve these targets. Results will be reviewed and improvements made, when required. - We will use a quality management system to investigate accidents and complaints, implement countermeasures, and manage conditions until they are resolved.
Employees comply with our code of conduct regarding environmental conservation, the prohibition of unfair trading, protection of personal information, and all other similar requirements.
Quality Maintenance and Management System
Promoting Good Distribution of Pharmaceuticals
Otsuka Warehouse has set up the GDP1 Promotion Office to facilitate appropriate logistics in accordance with the GDP guidelines for pharmaceuticals. We disseminate the principles of the GDP guidelines among personnel engaged in the manufacture and distribution of pharmaceuticals through training and drills on temperature control during shipping and storage, security and other quality management systems, document control, administration of outsourced processes, facility and equipment maintenance, storage and transport operations, assessment of supplier and customer eligibility, among others. In addition, we conduct regular training to ensure compliance with internal standards and procedures.
1: Good Distribution Practice
Measures to Enhance Distribution Quality
Systemization of Warehouse Operations2
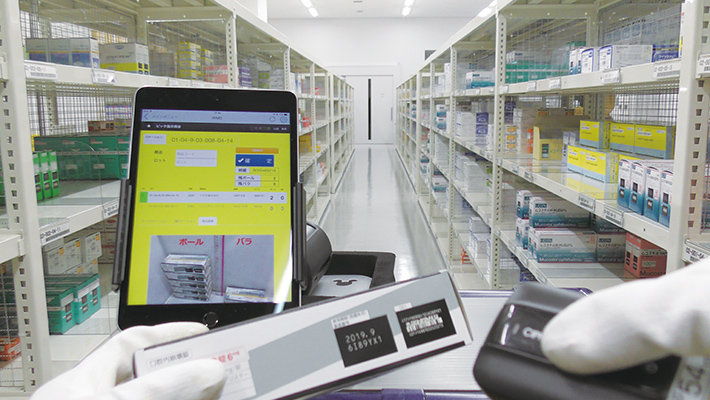
Otsuka Warehouse has shifted to a paperless environment through the use of tablets. The introduction of this information technology has enabled anyone to work effectively in warehouse operations, reducing delays and mistakes. Warehouse conditions can now be determined in real time, which is not possible with conventional paper-based picking systems. This minimizes inaccurate shipments and picking errors, leading to improved work efficiency and quality.
2: ID Warehouse (Otsuka Warehouse) (Japanese version only)
Understanding Delivery Status in Real Time3
Delivery operations that are difficult to visualize can restrict the work flow, leading to long work hours, among other negative effects. Otsuka Warehouse standardizes specifications for the data management system to simplify collaboration and cooperation between shippers and logistics operators. Introducing IT systems for dispatching trucks and vehicle monitoring enables better tracking of transportation and delivery as well as improves the quality of logistics. At the same time, AI is used to visualize delivery operations, such as automatically recommending a delivery route, in line with the goal of streamlining work and increasing the quality of logistics.
3: ID Transport (Otsuka Warehouse) (Japanese version only)
Measures to Maintain a Stable Supply
Establishing the BCP System
Otsuka group companies coordinate with Otsuka Warehouse to ensure a stable supply of products so that business can continue to the extent possible even during a largescale earthquake or other disaster. Business continuity is aided by having logistics sites throughout Japan, diversified production inventory, and a robust nationwide network of sites based on securing new locations.
Furthermore, for pharmaceuticals, a framework for business continuity planning (BCP) has been established that ensures essential products can be delivered to where they are needed. In addition to securing stock, measures include developing an emergency response system for transporting products, for example registering vehicles for authorized access to restricted areas and exchanging MOUs with shippers, warehouse owners and other partners for cooperation in the transport of emergency relief supplies.
Key Base for BCP: West Japan Logistics Center (Otsuka Warehouse)
Since 2015, Otsuka Warehouse has been operating the West Japan Logistics Center in Kobe City, Hyogo Prefecture—around two hours from Tokushima, where the main Otsuka group factories are located. The ground in the area is hard and there is a low probability of a major earthquake. By installing private emergency power generation equipment that can operate 24 hours a day even during a power outage due to an earthquake or other disaster, the Center can operate at full capacity for around three days. In addition, the quake-absorbing building structure can withstand a largescale earthquake or tremors. For this reason, we have created a BCP system, where supply can continue, by stopping products from falling and being damaged, and buildings are prevented from collapsing.
-
West Japan Logistics Center -
Emergency private power generation facilities -
Seismic isolation system
Environmentally Friendly Distribution
Reducing CO2 Emissions
Among measures to reduce environmental impact, Otsuka Warehouse is moving forward with a modal shift to rail and sea transportation, which have lower CO2 emission intensities. Use of a reservation system for booking access times when receiving and shipping at warehouses has reduced the average waiting time for drivers by more than half. Such measures contribute to reducing CO2 emissions throughout the industry. Further, considering the optimal vehicles and routes for diverse products and transport destinations, the company is implementing joint logistics, which combines products from multiple companies in a single vehicle, in this way reducing the number of transportation vehicles across society.
Details here(Japanese version only)
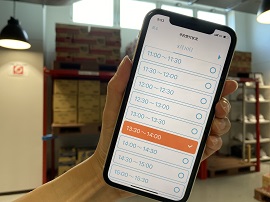
Truck Reservation System
Otsuka Warehouse uses IT to increase efficiency in warehouses, connecting them to pre- and post-distribution operations. Drivers can connect with each warehouse and get an overall picture of logistics online in a system known as connected logistics. The aim is to resolve some of the issues that have plagued the logistics industry. A truck reservation system makes it possible to make reservations for unloading times online, in this way seriously reducing driver wait times, contributing to lower CO2 emissions as well as improving the work environment for drivers and addressing the issue of a shortage of drivers and vehicles.