Core Principles
The Otsuka group recognizes that ensuring safety and health across all of its business activities is an important element of the management. This recognition is based on our corporate philosophy of “Otsuka-people creating new products for better health worldwide.” Accordingly, we strive to ensure all workplaces are safe and healthy, including by offering education and training for all concerned.
Otsuka Group Health and Safety Policy
- Based on our recognition that ensuring safety and health is an important element of the management, we are committed to ensuring that each and every one of us proactively engages in safety and health activities, and we work together to create safe, healthy, and comfortable workplaces across the entire group.
- We comply with the relevant laws and regulations of each country and region, as well as the voluntary management standards of each company and site.
- We strive to prevent the expansion of damage and/or recurrence of accidents by practicing ongoing risk reduction activities such as forecasting, ascertaining, and periodically reviewing dangerous and hazardous factors, responding promptly and appropriately in the event of an emergency such as an industrial accident, and subsequently sharing lessons learned within the organization.
- We request an understanding of our Policy and the promotion of health and safety awareness by all the business partners of the Otsuka group (including contractors, and suppliers, etc.)
Group-wide targets
■ Goals of health and safety action plan
・Zero occupational accidents
- Please refer to Health and Productivity Management for comprehensive goals regarding health management.
■ Progress
・Rate of occupational accidents: 1.20 (2023 result)
・Severity of occupational accidents: 0.01 (2023 result)
- Refer to Key Sustainability Data for details.
Promotion System for Health and Safety
In accordance with its corporate philosophy, the Otsuka group stresses ensuring the safety and health in all its business activities. Business sites are required by law to have a Health and Safety Committee, regularly hold meeting of the committee, identify sources of risk and conduct risk assessments, and strive to maintain a safe work environment. For example, Otsuka Holdings, Otsuka Pharmaceutical, and Otsuka Medical Devices, which conduct business from the same business site (Tokyo), undertake activities to improve the workplace environment, which includes holding monthly joint Health and Safety Committee meetings and conducting seminars and sharing information in line with that topic. The Production Division has been holding a group-wide Global Production Conference for more than thirty years. At this conference, information on work accidents, production technology, and quality are shared and efforts are made to improve technology throughout the whole global organization.
- Refer toProduction for details of the Global Production Meeting.
Since each group company employs a different promotion system, the one for Otsuka Pharmaceutical is shown here.
Otsuka Pharmaceutical’s Promotion System for Health and Safety (Production Division)
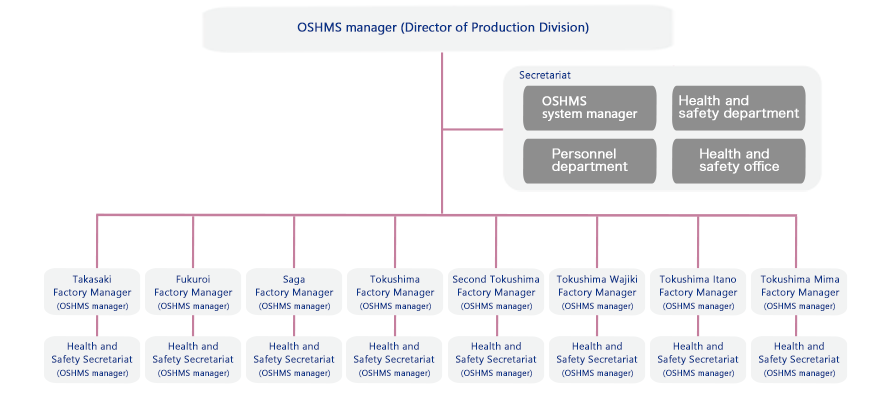
Otsuka Pharmaceutical has established an OSHMS*and will continue to improve the workplace environment based on company-wide policies.
*OSHMS (Occupational Safety and Health Management System) is a set of measures for safety and health management aimed at preventing occupational accidents, promoting the health of workers, creating a comfortable work environment and improving the safety and health standards of workplaces. These objectives are achieved by establishing a series of procedures and voluntarily conducting ongoing safety and health management based on a PDCA (plan-do-check-act) cycle implemented by a business with the cooperation of employees.
Approach
Evaluating and Addressing Risk
Safety and health committees have been established at locations where they are legally required. These committees meet regularly to discuss safety and health and how to maintain a safe work environment. In addition, information is shared on risk assessments at regular meetings to identify sources of risk.
For example, Otsuka Pharmaceutical annually assesses risk by identifying occupational health and safety issues associated with new tasks, testing methods, manufacturing processes, and other activities at business sites. Risk assessments are used to find potential dangers or hazards in the workplace and to eliminate or reduce them. For each issue identified, we provide a written follow-up on the measures we implemented. We confirm that the risk has been mitigated in the risk assessment in the following fiscal year. In addition, we are working to reduce occupational health risks and improve the workplace environment by sharing information on social demands and onsite problem awareness, led by the person in charge of health and safety.
Human Resource Development and Education System
The Otsuka group conducts training related to occupational health and safety. In addition to regular training according to annual plans at each company, we also carry out education on company and factory rules as well as training on safety, health, and environmental matters, as well as on manufacturing and quality control related to products and their production processes.
Otsuka health and safety education at Otsuka Pharmaceutical’s Tokushima Factory in 2024 (excerpts)
Type of education | Target (number of people to be trained) | Frequency of training |
---|---|---|
Occupational Safety and Health Management System Internal Auditor Training | New Safety and Health Promotion Committee Member/Officer (approximately 10) | Once a year |
KYT* training | All employees at the Tokushima Factory (approximately 320) | 6 times a year |
Chemical substances education and information | All employees at the Tokushima Factory (approximately 320) | 12 times a year |
Video-based health and safety education | All employees at the Tokushima Factory (approximately 320) | 12 times a year |
Safety and health education through immersive VR (virtual reality) simulations | 40 applicants | Once a year |
JFE Steel Safe Physical Fitness™ Functional Tests and Improvement Measures | Employees over the age of 30 (approximately 100) | Once a year |
- *(kiken yochi training) stands for kiken (hazard (K)), yochi (prediction (Y)), and training (T), meaning hazard prediction training
Status of Occupational Accidents
2020 | 2021 | 2022 | 2023 | |||||
---|---|---|---|---|---|---|---|---|
Rate of occupational accidents | Severity of occupational accidents | Rate of occupational accidents | Severity of occupational accidents | Rate of occupational accidents | Severity of occupational accidents | Rate of occupational accidents | Severity of occupational accidents | |
Otsuka group | 1.11 | 0.00 | 0.70 | 0.02 | 0.56 | 0.00 | 1.20 | 0.01 |
Industry-wide | 1.95 | 0.09 | 2.09 | 0.09 | 2.06 | 0.09 | 2.14 | 0.09 |
- Please also refer to Key Sustainability Data
The Otsuka group shares examples of occupational accidents that have occurred at group companies (production and research departments) through meetings held to exchange information on safety and health.
Communication Beyond the Company
Otsuka Pharmaceutical conducts a range of programs both inside and outside the Company to promote workplace health and safety. One example is an annual meeting to share workplace health and safety information with partner companies.
Occupational Health and Safety Information Exchange Meeting
*Not held in 2021 due to the COVID-19 pandemic.
Topic | |
---|---|
2019 | 15th “Safety and health activities in the first year of work style reform: Contributing to productivity improvement and health management” |
2020 | 16th “Stress management under the new lifestyle: How to deal with” |
2022 | 17th “Self-regulated chemical management considering new chemical regulations” |
2023 | 18th “Back to Basics – Revisiting Our Foundations to Prevent Workplace Accidents” |
2024 | 19th “Disaster Prevention Activities: Protect Companies, Employees, and Families” |
Supplier Occupational Safety and Health
The Otsuka group recognizes the importance of ensuring occupational safety and health at suppliers in the Otsuka Group Sustainable Procurement Guidelines. Specifically, we request that they respect human rights, ensure a safe, hygienic and comfortable work environment, and consider the health of employees. We hold briefings every year to help our suppliers understand the detailed content of the guidelines and have received written consent from all suppliers stating agreement with their objectives. The Otsuka group will continue to work together with suppliers to ensure occupational safety and health.
- Refer to Procurement for more details.
Company Involvement in Commitments to Labor Standard Initiatives or Frameworks
Example: Tokushima
- Tokushima Labor Standards Association [Otsuka Pharmaceutical, Taiho Pharmaceutical, Otsuka Warehouse, Otsuka Chemical, Otsuka Foods, etc.]
Regional association: Tokushima Labor Standards Association Union Meeting - Naruto Labor Standards Association [Otsuka Pharmaceutical, Otsuka Pharmaceutical Factory, etc.]
- Anan Labor Standards Association [Otsuka Pharmaceutical, Otsuka Techno]
- Miyoshi Labor Standards Association [Otsuka Pharmaceutical]
Improvement Case Study
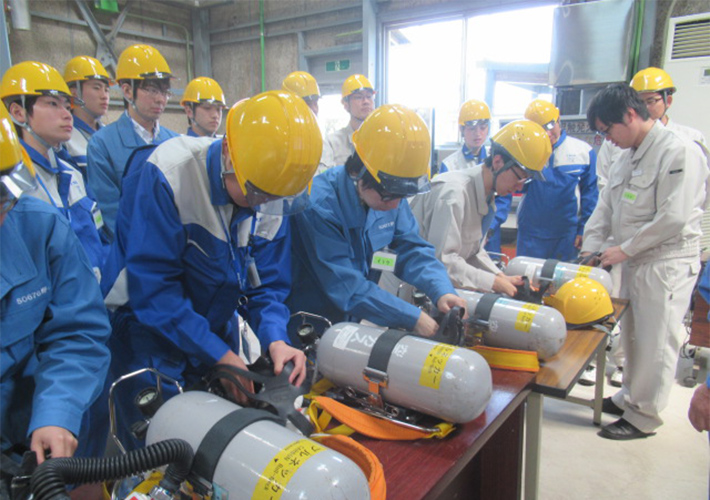
Otsuka Chemical, which handles chemical substances, conducts various workplace safety initiatives. Major initiatives include a system for swift information sharing on issues related to factory operations among all domestic and overseas locations, as well as regular reporting of group safety at Board of Directors meetings. Another key initiative is Anzen Dojo, an experience-based safety training center which opened in 2012 as part of measures to prevent occupational accidents. The center runs training programs aimed at improving safety awareness for group employees, employees of overseas affiliates, and third parties. Through classroom instruction and simulations of past accidents, the center reinforces lessons from failures and safety knowledge, sharpens awareness of danger, and develops the ability to identify potential risks. In recognition of its activities to improve health and safety education and establish a safety culture through Anzen Dojo, Otsuka Chemical received an RC Outstanding Award from the Japan Chemical Industry Association at the 8th Annual Responsible Care Awards in 2014.